Expertos de la Escuela de Ingenierías Industriales han firmado varios trabajos científicos sobre el acero para entender mejor el comportamiento y resistencia de este y de otros metales desarrollados a partir de esta técnica
La gran mayoría de los materiales son duros y resistentes, o bien maleables y dúctiles. Sin embargo, los aceros, y en concreto el acero maraging tienen muy buena dureza y resistencia, y además son maleables. Por ello este metal, generalmente conformado de aleaciones de hierro-níquel, se utiliza en muchas aplicaciones en las que los requerimientos son extremos, como la aeronáutica y la automoción, pero también en piezas e instrumental que pueden resultar más familiares como palos de golf, utensilios de cirugía e incluso armas de esgrima, en la que se aplica la variante 18Ni300 de esta aleación para otorgar al florete una excelente resistencia a la fractura.
Ahora un grupo de investigación de la Universidad de Málaga ha dado un paso más en la comprensión de los defectos internos de este acero. En concreto, gracias a la tomografía computarizada de rayos X (XCT) han logrado visualizar y cuantificar la porosidad interna de muestras típicamente empleadas en pruebas de resistencia. Así lo recoge el trabajo publicado en la revista Materials centrado en el análisis de los poros formados después de la fabricación y en la definición de otros parámetros clave como la esfericidad, la relación de aspecto, la superficie y el volumen.
El doctor Pablo López Crespo, investigador de Departamento de Ingeniería Civil, de Materiales y Fabricación y responsable del estudio, señala que una de las novedades que aporta el análisis en tres dimensiones que han utilizado es que "gracias a este método se superan los inconvenientes de otras técnicas convencionales 2D, ya que estas solo proporcionan mediciones superficiales y, por lo tanto, información incompleta".
En concreto, los investigadores del grupo Comportamiento y Procesado de Materiales de la Universidad de Málaga han llevado a cabo un estudio que relaciona la resistencia a la fractura por fatiga con la porosidad interna que presenta el metal obtenido mediante lo que se denomina "fabricación aditiva", más conocida como impresión 3D. Este nuevo método de fabricación de materiales se ha extendido considerablemente a los metales en los últimos cinco años, gracias, entre otras ventajas, a que permite obtener formas complejas y personalizar diseños en todo tipo de manufactura de manera rápida y económica. "Además, añade López Crespo, se reduce drásticamente la cantidad de material utilizado en comparación con procesos más estándares, como el mecanizado, lo que contribuye al uso más razonable y sostenible de las materias primas".
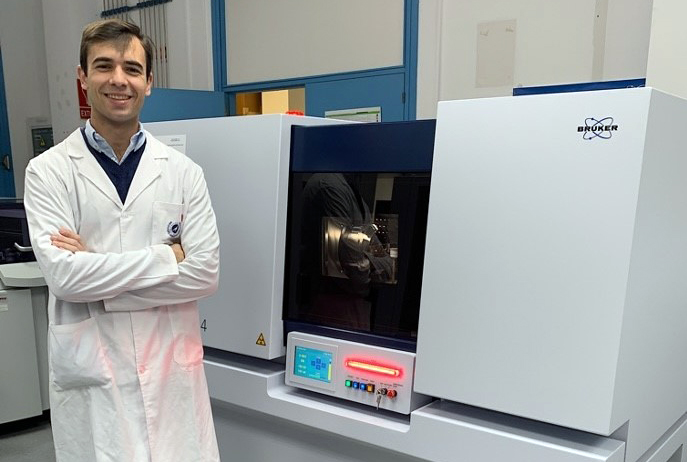
El investigador Pablo Moreno Cerezo, uno de los autores de la investigación, junto al equipo de tomografía axial computarizada (TAC) para descubrir si hay poros en el interior de las piezas de metal.
Un viaje al interior del acero
En pleno proceso de expansión de la impresión 3D para fabricación de metales, una variable clave es determinar con exactitud cómo afecta a las propiedades de las piezas metálicas obtenidas con esta técnica, ya que, como reconocen los expertos "a menudo se generan poros internos que empeoran el comportamiento del material".
Para ello se han analizado distintas direcciones de impresión mediante espectroscopía de rayos X, microscopía electrónica de barrido y metalografía. Además, se ha utilizado la técnica de tomografía axial computarizada —los conocidos TACs que se utilizan en diagnóstico médico—. De modo que al igual que los TACs permiten ver el interior del cráneo o el tórax, también permiten visualizar la distribución interna en los metales, descubrir los poros que hay en el interior de la pieza y medir su forma y su tamaño.
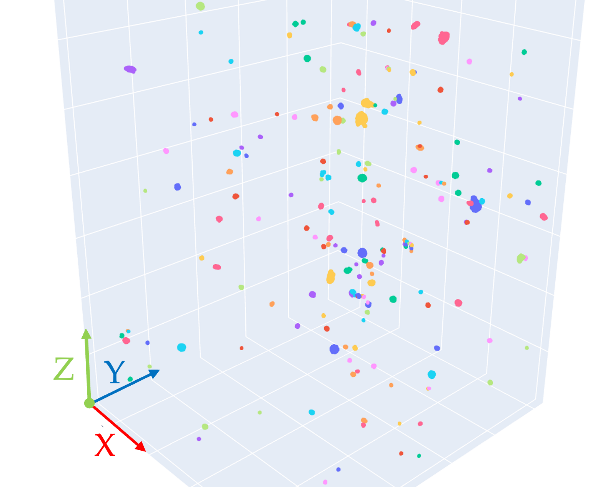
Distribución de poros en el interior de la probeta de acero. La técnica de tomografía se ha usado para conocer el interior del material opaco, y permite ver la posición, la forma y el tamaño de los defectos internos en el material.
Los hallazgos del estudio revelan que la mayoría de los poros son producidos por gases atrapados en el proceso de fabricación. Por ello estos parámetros son clave a la hora de entender cómo de fiable es una pieza antes de usarla. "Sobre todo si se relaciona la porosidad interna del material con la resistencia a fractura por fatiga", explica el profesor de la UMA, que junto a su equipo han constatado en el laboratorio que la porosidad se reduce si el material se imprime en unos ángulos determinados. Los resultados concluyen que los poros se reducen en caso de imprimir el acero a 0º o a 90º, pero no a 45º, debido a que esta inclinación aumenta el volumen de poros y con ello aumentan considerablemente las probabilidades de fractura.
A partir de este hito la tomografía de rayos X, combinada con técnicas de microscopía óptica, proporciona una imagen completa de la porosidad interna del acero y de otros metales. "Consideramos que este avance debe traducirse tanto en el ámbito académico como en el industrial en un impulso de cara a optimizar la calidad del material y ampliar sus aplicaciones de alta exigencia que se demandan en este sector", concluye López Crespo.
Cerezo PM, Aguilera JA, Garcia-Gonzalez A, Lopez-Crespo P. Influence of Porosity on Fatigue Behaviour of 18Ni300 Steel SLM CT Specimens at Various Angles. Materials. 2024; 17(2):432. https://doi.org/10.3390/ma17020432
Cerezo PM, Aguilera JA, Garcia-Gonzalez A, Lopez-Crespo P. Tomography of Laser Powder Bed Fusion Maraging Steel. Materials. 2024; 17(4):891. https://doi.org/10.3390/ma17040891